I started this build around 15 months ago with no welding experience. I did a good bit of research and looked at a lot of builds and came up with an idea of what i wanted to build mine like. I did this build on a budget and luckily i was able to get everything very cheap and some for free. Between that, my daughter being born, and not having any big tools to do the cutting or lifting , it took me a while to finish. All i had for this project was a Hobart Handler 180 mig welder, a Dewalt angle grinder, and an electric drill. I followed the bbq calculator on the smoke ring forum to a T.
I needed a trailer but was unable to find one for a good price. Luckily a very good friend had 31ft of this 4"x4" square tubing he didn't want so that is what i used for my trailer. I was able to find an axle from an old mini van for 40 bucks and off i went building the trailer.
Another friend of mine gave me this 2"x4" tubing. It was only 10 ft long but i was able to use part of it for the tongue and the rest for a support to tie the tongue into the trailer frame
Getting the tank on the tank on the trailer was tricky with no hoists or other tools. I waited until my brother was able to come over and help. We put a t-post through the hook on the front of the tank and were able to pick the front end up and set it on the trailer and then gradually slide the tank onto the supports. The tank was HEAVY!!! You can tell by the t-post being bent like out of shape.
I decided to go with 2 doors because of the sheer weight of each door. 1 big door would be too much. I marked off my doors with some chalk. I marked to top of the doors about 3" down from the 12:00 mark and the bottom of the door about 1" below the 3:00 mark. That way with my 1" tubing , the top of the grate would be at the center 3:00 mark.
Next i cut the doors out very slowly. I left 2" at every corner and the center of each side. I was worried the cutting out the doors too fast would cause the tank to "spring". I had read about this happening and i knew i didnt have the tools to fix a problem like that,,,luckily my plan worked and the doors came out fine. Next i welded some 1 1/2" flatbar around the edges of the doors. I decided to make my own hinges out of some 1/4" steel plate scrap. Nothing fancy just drilled a 5/16" hole in each hinge and welded a small piece of 5/16" round stock in place. I did order some spring handles. I liked the look of them in other builds and had no way to fabricate any so i bought 5 handles. I ended up cutting some more 1/4" plate and running some scrap rebar i had laying around through the spring and welded into place.
A family member of mine is in the well drilling business and i was able to get a few pieces of 6" scrape pipe to use for my smoke stack. I was glad to get my hands on 6" instead of 4" because 4" would have to be too tall. Cutting out a round hole on the edge of the tank with a angle grinder was probably one of the most aggravating parts of the build. Not only was it tough but fitting the pipe was tough as well. Eventually i got fitted perfectly.
Through my research of reverse flow smokers i found the majority of the reverse flow plates are welded 3"-5" below the grates. I decided to have my reverse flow plate 4" below my grate so i found the center line at the end of the tank and marked a line for my cut for the firebox.
Next i had to weld in the supports for the reverse flow plate. I ended up using some 1" square tubing.
Fitting the reverse flow plate was very tough. I used some 1 1/2" angle for my drip channel so i cut my plate in 2 equal pieces. Each piece of plate weighed close to 100 pounds a piece and moving it by myself was tough so i tack welded some u-bolts in place for handles. That helped and i was able to fit them and tack them in place.
I landed the plate for my firebox at a scrap yard. It was an odd shapes piece but it was 3/8" and big enough for me to get (6) 27 1/4" square pieces , which worked out great because it was just about the exact size the bbq calculator called for. I beveled all the sides and welded into place. My grinder cut off wheels wouldnt touch this plate so i took the plate by a fab shop and they used a huge metal shear to cut the plate and also cut out the intake holes for me. I didnt have a way to make a 2" cut with my grinder so i got them to. I never thought i would finish welding this firebox. It was like the never ending weld. This firebox is HEAVY!!!
I had no way to lift the firebox up to weld it to the tank so i had my neighbor lift it up with his tractor and hoist. I used flat black rust oleum paint. It took me a while to come up with a firebox latch handle design. I wanted something with a latch because they looked the best to me so i uses some scrap 1/4" and some left over 5/16" round stock. I welded a cutoff piece of rebar to the 1/4" stick and slipped a spring handle over it. I also decided to go with the same hinge design as i did with the tank doors.
I had some angle left over so i welded some supports on the inside of the firebox door. I was worried it would warp if it got too hot
This was one heck of a project. If i had a plasma cutter it would have been sooo much easier. I nought a brand new dewalt grinder at the beginning of the project and burnt it up about 3 weeks ago. I limped to the finish line with a 29 dollar harbor freight grinder. I am going to add a fold out table the front of the tank at some point in the near future. I sprayed the inside of the tank and grates with pam spray for seasoning and ran a hot fire for 5 hours today. It sure was a GREAT feeling to see that smoke rolling out of the stack. The temps were good. I got it as high as 500 degrees and once i dialed it down to the mid 200's towards the end i only had a 12 degree difference from the front to the back. My first smoke on it will be some Christmas turkeys.
I needed a trailer but was unable to find one for a good price. Luckily a very good friend had 31ft of this 4"x4" square tubing he didn't want so that is what i used for my trailer. I was able to find an axle from an old mini van for 40 bucks and off i went building the trailer.
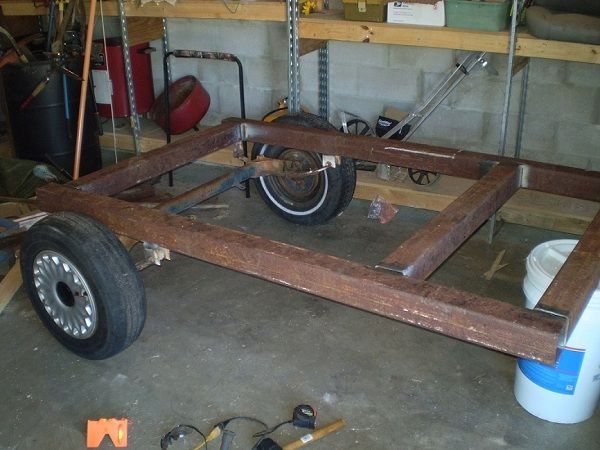
Another friend of mine gave me this 2"x4" tubing. It was only 10 ft long but i was able to use part of it for the tongue and the rest for a support to tie the tongue into the trailer frame
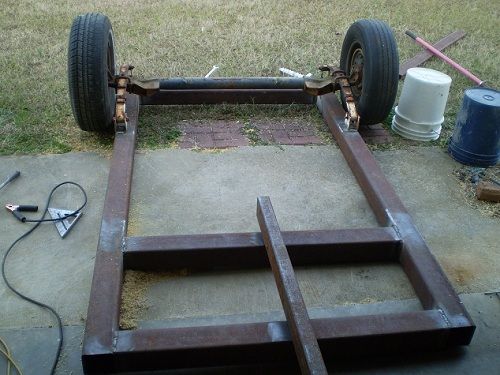
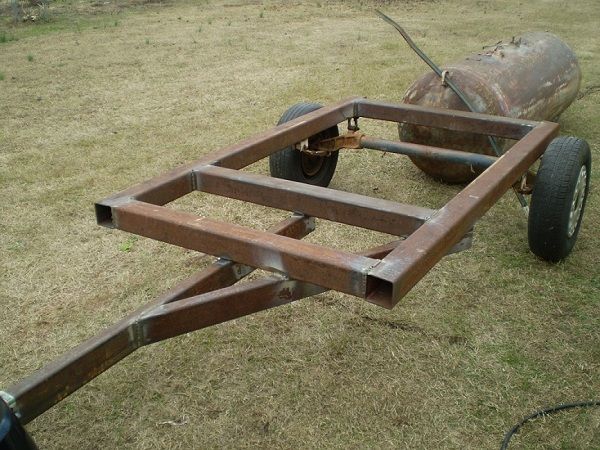
Getting the tank on the tank on the trailer was tricky with no hoists or other tools. I waited until my brother was able to come over and help. We put a t-post through the hook on the front of the tank and were able to pick the front end up and set it on the trailer and then gradually slide the tank onto the supports. The tank was HEAVY!!! You can tell by the t-post being bent like out of shape.
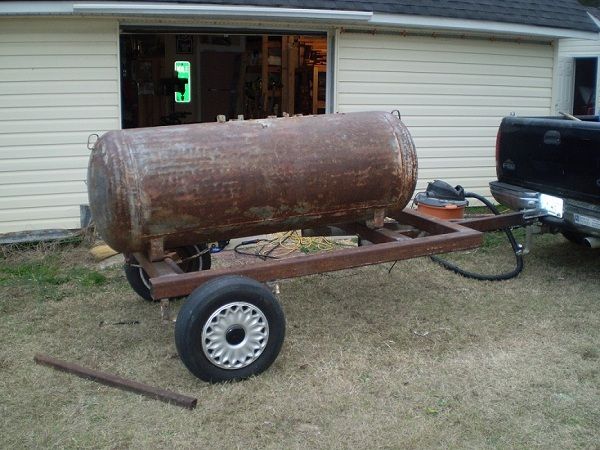
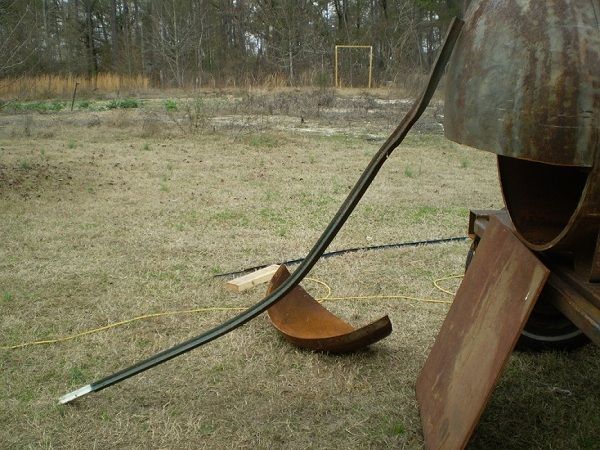
I decided to go with 2 doors because of the sheer weight of each door. 1 big door would be too much. I marked off my doors with some chalk. I marked to top of the doors about 3" down from the 12:00 mark and the bottom of the door about 1" below the 3:00 mark. That way with my 1" tubing , the top of the grate would be at the center 3:00 mark.
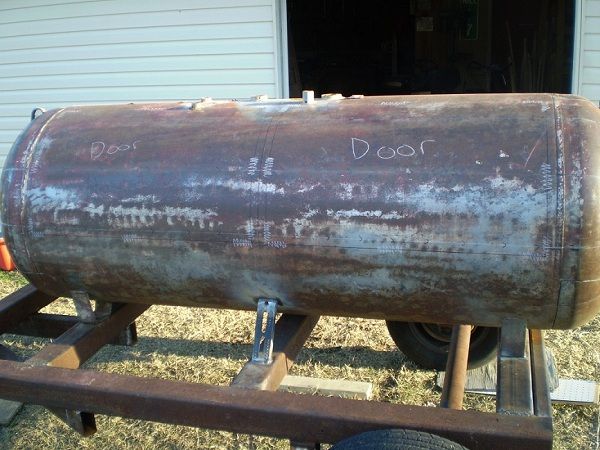
Next i cut the doors out very slowly. I left 2" at every corner and the center of each side. I was worried the cutting out the doors too fast would cause the tank to "spring". I had read about this happening and i knew i didnt have the tools to fix a problem like that,,,luckily my plan worked and the doors came out fine. Next i welded some 1 1/2" flatbar around the edges of the doors. I decided to make my own hinges out of some 1/4" steel plate scrap. Nothing fancy just drilled a 5/16" hole in each hinge and welded a small piece of 5/16" round stock in place. I did order some spring handles. I liked the look of them in other builds and had no way to fabricate any so i bought 5 handles. I ended up cutting some more 1/4" plate and running some scrap rebar i had laying around through the spring and welded into place.
A family member of mine is in the well drilling business and i was able to get a few pieces of 6" scrape pipe to use for my smoke stack. I was glad to get my hands on 6" instead of 4" because 4" would have to be too tall. Cutting out a round hole on the edge of the tank with a angle grinder was probably one of the most aggravating parts of the build. Not only was it tough but fitting the pipe was tough as well. Eventually i got fitted perfectly.
Through my research of reverse flow smokers i found the majority of the reverse flow plates are welded 3"-5" below the grates. I decided to have my reverse flow plate 4" below my grate so i found the center line at the end of the tank and marked a line for my cut for the firebox.
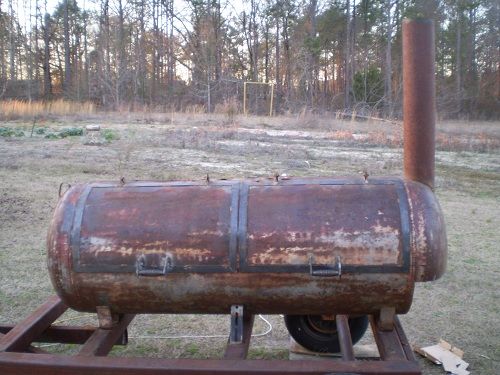
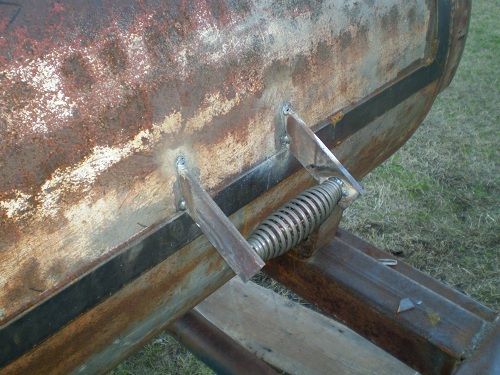
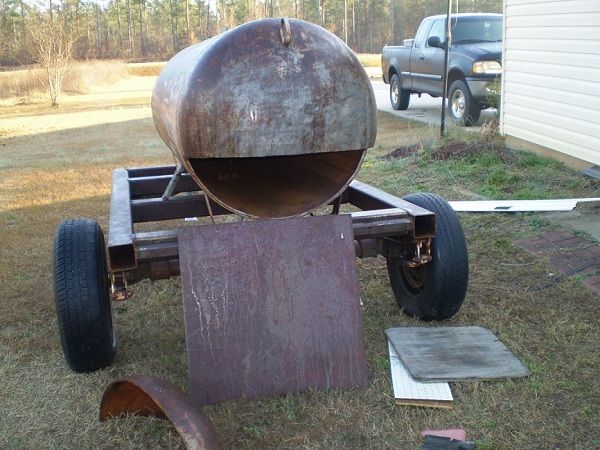
Next i had to weld in the supports for the reverse flow plate. I ended up using some 1" square tubing.
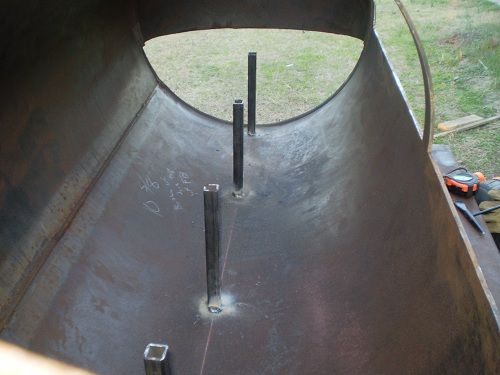
Fitting the reverse flow plate was very tough. I used some 1 1/2" angle for my drip channel so i cut my plate in 2 equal pieces. Each piece of plate weighed close to 100 pounds a piece and moving it by myself was tough so i tack welded some u-bolts in place for handles. That helped and i was able to fit them and tack them in place.
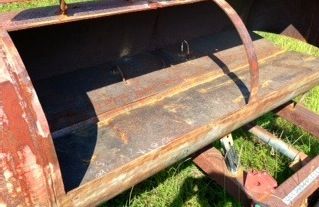
I landed the plate for my firebox at a scrap yard. It was an odd shapes piece but it was 3/8" and big enough for me to get (6) 27 1/4" square pieces , which worked out great because it was just about the exact size the bbq calculator called for. I beveled all the sides and welded into place. My grinder cut off wheels wouldnt touch this plate so i took the plate by a fab shop and they used a huge metal shear to cut the plate and also cut out the intake holes for me. I didnt have a way to make a 2" cut with my grinder so i got them to. I never thought i would finish welding this firebox. It was like the never ending weld. This firebox is HEAVY!!!
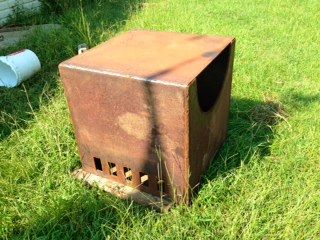
I had no way to lift the firebox up to weld it to the tank so i had my neighbor lift it up with his tractor and hoist. I used flat black rust oleum paint. It took me a while to come up with a firebox latch handle design. I wanted something with a latch because they looked the best to me so i uses some scrap 1/4" and some left over 5/16" round stock. I welded a cutoff piece of rebar to the 1/4" stick and slipped a spring handle over it. I also decided to go with the same hinge design as i did with the tank doors.
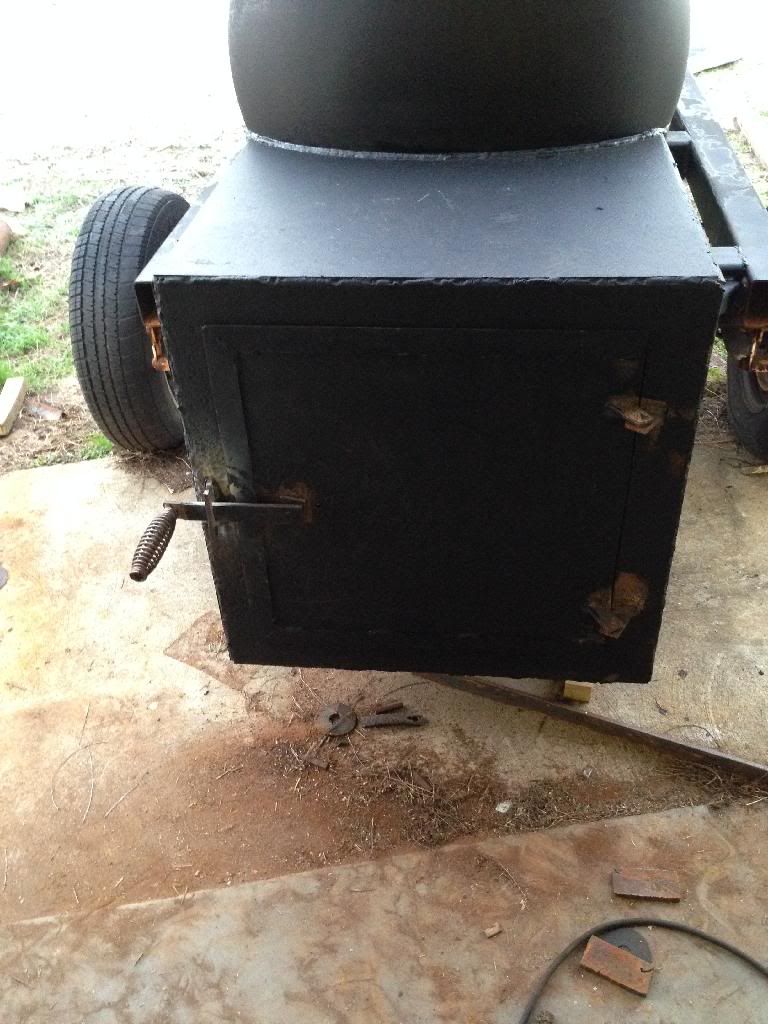
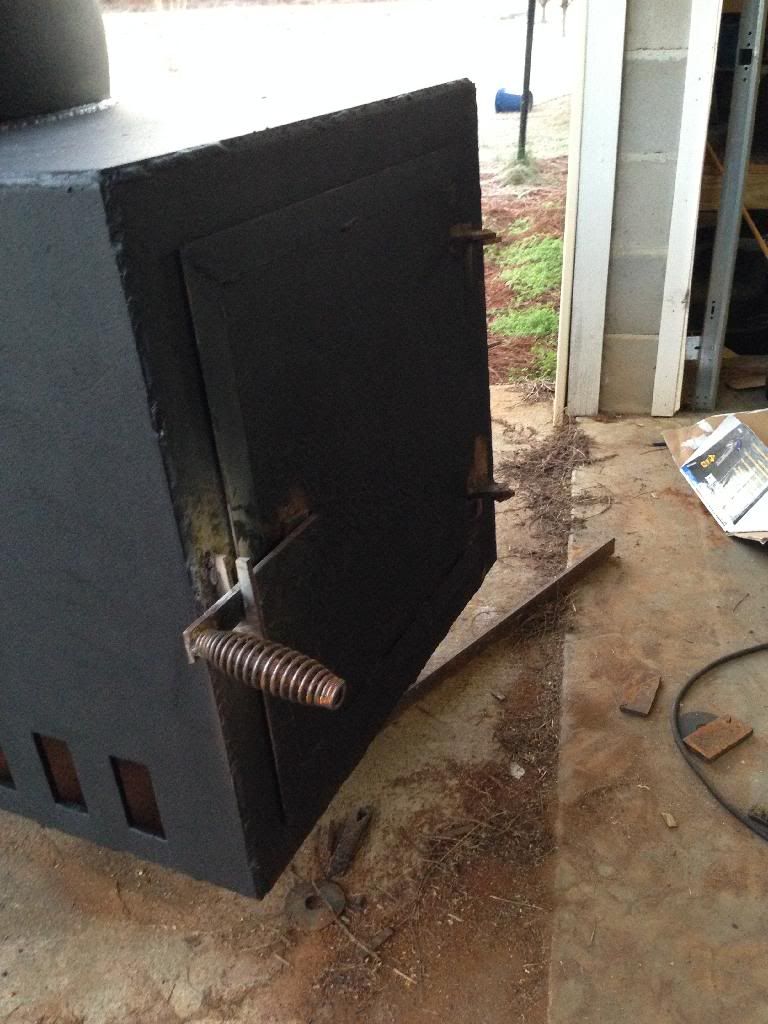
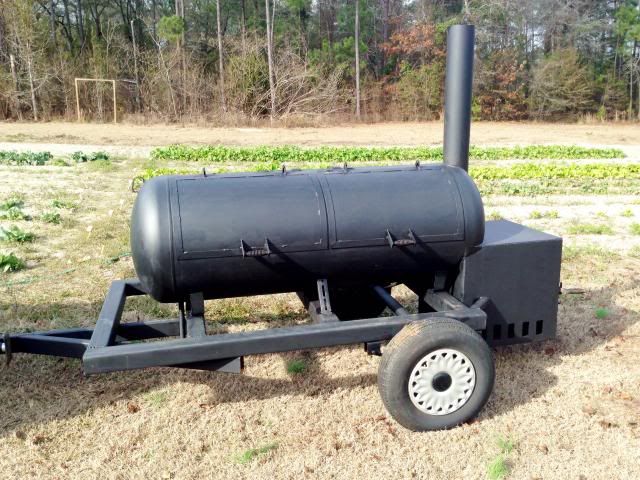
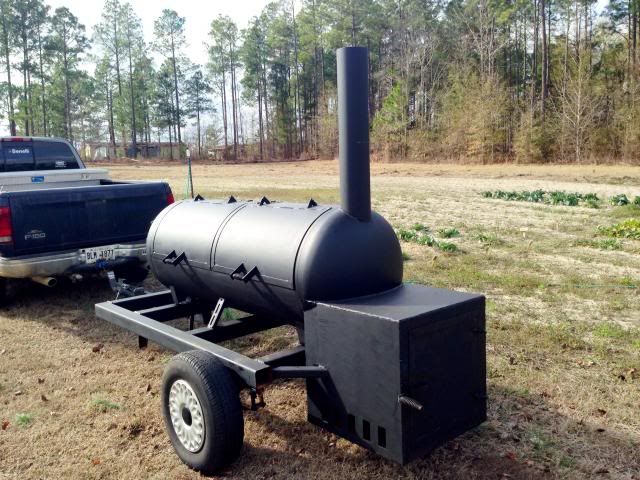
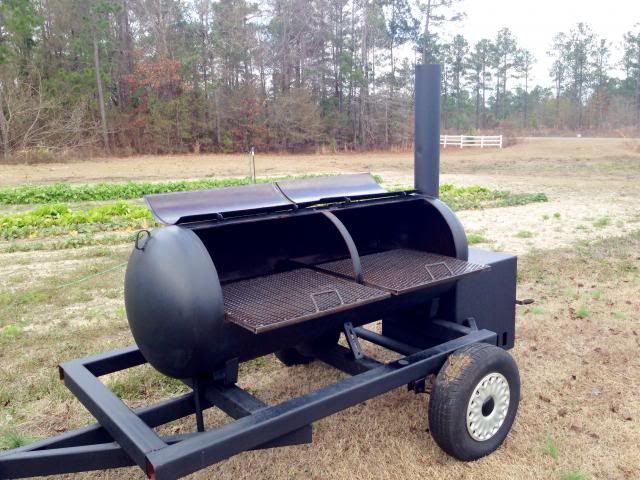
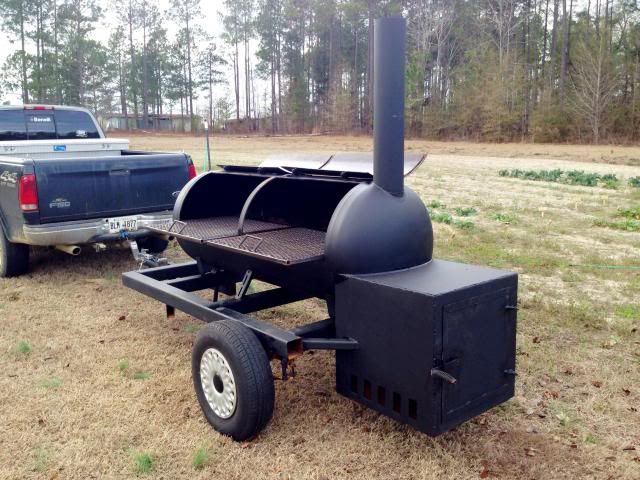
I had some angle left over so i welded some supports on the inside of the firebox door. I was worried it would warp if it got too hot
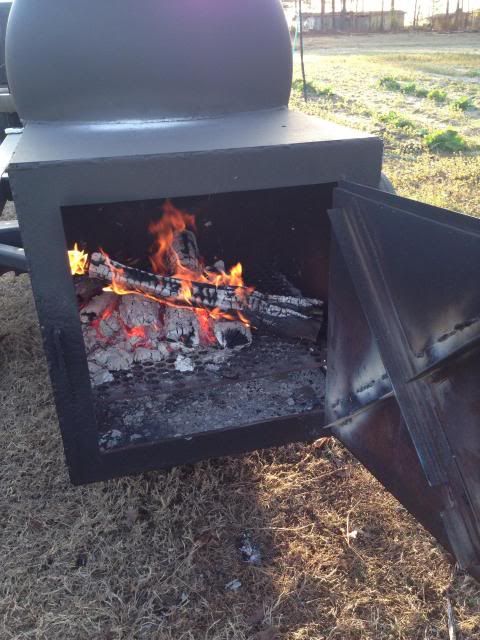
This was one heck of a project. If i had a plasma cutter it would have been sooo much easier. I nought a brand new dewalt grinder at the beginning of the project and burnt it up about 3 weeks ago. I limped to the finish line with a 29 dollar harbor freight grinder. I am going to add a fold out table the front of the tank at some point in the near future. I sprayed the inside of the tank and grates with pam spray for seasoning and ran a hot fire for 5 hours today. It sure was a GREAT feeling to see that smoke rolling out of the stack. The temps were good. I got it as high as 500 degrees and once i dialed it down to the mid 200's towards the end i only had a 12 degree difference from the front to the back. My first smoke on it will be some Christmas turkeys.
Last edited: