I am new here and looking to contribute. I am not sure this is the correct place to post this but I hope it is. I have seen several posts about holsters so I figured I would put up this tutorial to help anyone interested in making their own.
Disclaimer, I am only a hobbyist. I am doing this tutorial to help others in making their own Kydex holsters.
So you may have purchased a holster from some company for $50-$100. We have all been there; however if you are like me, you have more guns than holsters. Dropping another $100 every time you get a gun or add a tactical light or whatever can get costly. Worse is if you have some combination of light and gun that no one makes a holster for, or you have to give them your gun for a week for them to make the holster. This is what eventually forced me to learn how to make a quality Kydex holster. So once you get the basics down, you can make a holster, sheath, or whatever with Kydex. I figured that since I have seen several posts about what holster to get I would do this tutorial.
Up front you will need some tools and supplies but once this is acquired, you can produce a quality holster for about $10-$15. Most of these tools can be purchased from Harbor Freight, Northern Tool, etc… and are often on sale.
The basic tools:
Retractable Utility Knife ($5.00)
Metal Ruler ($2.00)
Non-contact Infrared Thermometer ($30.00)
Leather Work Gloves ($20.00)
Drill with ¼” Drill Bit ($30.00)
Heat Gun ($22.00)
Toaster Oven ($20.00)
¼” eyelet hand setter ($12.00)
Hammer ($10.00)
Kydex Press ($30.00-$40.00) You will need to build this, see below
Belt loop jig ($20.00) You will need to build this, see below
These are the minimum tools you will need.
If you have the following tools it will make everything easier on you:
Drill Press
Belt Sander
Vice
Band Saw
Dremel
Perishables:
Medium-Grit Sanding Sponge ($8.00)
Blue Painters Tape ($2.00)
Wood Dowels Assorted Sizes ($10.00) Michel’s Craft store sells an assortment kit
Wood Craft Sticks ($5.00) Tongue Depressors
Materials:
So Kydex comes in different thicknesses, .60, .80, .93, and .125. I recommend using the .80 thickness and this tutorial is designed for this thickness. .80 is ideal for holsters and will deliver a good balance of definition and durability. For one typical holster you will need two pieces of Kydex at 9”x7” and another piece of 2”x6” for the belt loops. Kydex is sold in 12”x12” sheets but you can also buy it in bulk up to 4’x8’ sheets. I normally get 2’x4’ sheets and that lets me make several holsters. All the Kydex and hardware can be purchased from knifekits.com, diyholsters.com, or Amazon.
The hardware is determined by the thickness of the Kydex so for .80 Kydex you will need the following hardware:
Kydex .80 ($5.00-$30.00)
Eyelets #8-10 ¼” ($10.00)
8-32 Philips head .500 (1/2”) machine screws ($10.00)
8-32 Philips head .375 (3/8”) machine screws ($10.00)
¼” slotted pass through post ($10.00)
7/32” rubber tubing ($5.00) get this from an ACE hardware or similar shop and you will only need a few inches, I just go ahead and buy it in 2’ sections at a time. You will be cutting the tube in 1/8” sections. These slices will be silencers. This is cheaper and more customizable than using rubber washers or O-rings.
Kydex Press:
So you can buy a Kydex press for about $100.00 but I recommend you build your own. You will need to purchase two pieces of 8”x12”x1” thermoforming foam. Each piece cost about $10.00 from knifekits.com
http://www.knifekits.com/vcom/product_info.php?cPath=41_524&products_id=4290
Once you have the foam you can use plywood and some bar clamps to build the press. Here is a picture of the press I built.
Once I started this tutorial, I decided to upgrade my press. I used some flat 1.5”x14”x1/8” thick steel from home depot. I cut it to fit then I used two ½”x 6” lag bolts with nuts and washers. Once I got it all together, I can now use a cordless drill to squeeze the press. A word of caution, you want it to press tight but you do not want to crush the gun so I use the slowest setting on my drill and since I was already familiar with how much pressure I applied with the clamp press, I had a good idea of how much pressure to apply here. Here is a side view.
I recommend you build a horizontal press rather than a hinged press. A hinged press will apply force unevenly and I have found them to push objects out of alignment. I am sure you can find plans on the internet for building a press, I just knocked my press out without plans, it works great.
To be continued...
Disclaimer, I am only a hobbyist. I am doing this tutorial to help others in making their own Kydex holsters.
So you may have purchased a holster from some company for $50-$100. We have all been there; however if you are like me, you have more guns than holsters. Dropping another $100 every time you get a gun or add a tactical light or whatever can get costly. Worse is if you have some combination of light and gun that no one makes a holster for, or you have to give them your gun for a week for them to make the holster. This is what eventually forced me to learn how to make a quality Kydex holster. So once you get the basics down, you can make a holster, sheath, or whatever with Kydex. I figured that since I have seen several posts about what holster to get I would do this tutorial.
Up front you will need some tools and supplies but once this is acquired, you can produce a quality holster for about $10-$15. Most of these tools can be purchased from Harbor Freight, Northern Tool, etc… and are often on sale.
The basic tools:
Retractable Utility Knife ($5.00)
Metal Ruler ($2.00)
Non-contact Infrared Thermometer ($30.00)
Leather Work Gloves ($20.00)
Drill with ¼” Drill Bit ($30.00)
Heat Gun ($22.00)
Toaster Oven ($20.00)
¼” eyelet hand setter ($12.00)
Hammer ($10.00)
Kydex Press ($30.00-$40.00) You will need to build this, see below
Belt loop jig ($20.00) You will need to build this, see below
These are the minimum tools you will need.
If you have the following tools it will make everything easier on you:
Drill Press
Belt Sander
Vice
Band Saw
Dremel
Perishables:
Medium-Grit Sanding Sponge ($8.00)
Blue Painters Tape ($2.00)
Wood Dowels Assorted Sizes ($10.00) Michel’s Craft store sells an assortment kit
Wood Craft Sticks ($5.00) Tongue Depressors
Materials:
So Kydex comes in different thicknesses, .60, .80, .93, and .125. I recommend using the .80 thickness and this tutorial is designed for this thickness. .80 is ideal for holsters and will deliver a good balance of definition and durability. For one typical holster you will need two pieces of Kydex at 9”x7” and another piece of 2”x6” for the belt loops. Kydex is sold in 12”x12” sheets but you can also buy it in bulk up to 4’x8’ sheets. I normally get 2’x4’ sheets and that lets me make several holsters. All the Kydex and hardware can be purchased from knifekits.com, diyholsters.com, or Amazon.
The hardware is determined by the thickness of the Kydex so for .80 Kydex you will need the following hardware:
Kydex .80 ($5.00-$30.00)
Eyelets #8-10 ¼” ($10.00)
8-32 Philips head .500 (1/2”) machine screws ($10.00)
8-32 Philips head .375 (3/8”) machine screws ($10.00)
¼” slotted pass through post ($10.00)
7/32” rubber tubing ($5.00) get this from an ACE hardware or similar shop and you will only need a few inches, I just go ahead and buy it in 2’ sections at a time. You will be cutting the tube in 1/8” sections. These slices will be silencers. This is cheaper and more customizable than using rubber washers or O-rings.
Kydex Press:
So you can buy a Kydex press for about $100.00 but I recommend you build your own. You will need to purchase two pieces of 8”x12”x1” thermoforming foam. Each piece cost about $10.00 from knifekits.com
http://www.knifekits.com/vcom/product_info.php?cPath=41_524&products_id=4290
Once you have the foam you can use plywood and some bar clamps to build the press. Here is a picture of the press I built.
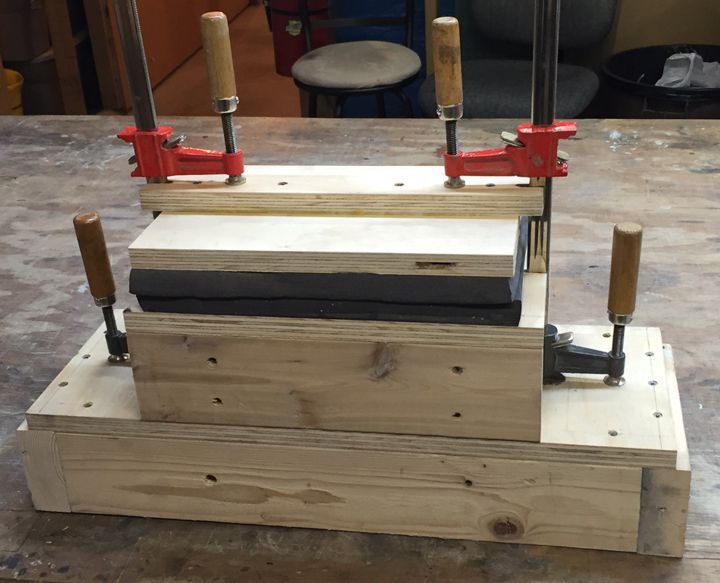
Once I started this tutorial, I decided to upgrade my press. I used some flat 1.5”x14”x1/8” thick steel from home depot. I cut it to fit then I used two ½”x 6” lag bolts with nuts and washers. Once I got it all together, I can now use a cordless drill to squeeze the press. A word of caution, you want it to press tight but you do not want to crush the gun so I use the slowest setting on my drill and since I was already familiar with how much pressure I applied with the clamp press, I had a good idea of how much pressure to apply here. Here is a side view.
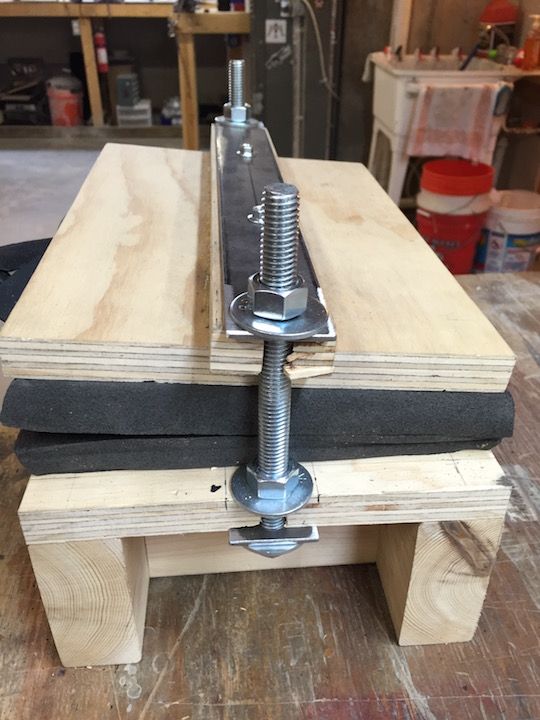
I recommend you build a horizontal press rather than a hinged press. A hinged press will apply force unevenly and I have found them to push objects out of alignment. I am sure you can find plans on the internet for building a press, I just knocked my press out without plans, it works great.
To be continued...